|
1. Adsorptive Media Trailer
This portable Adsorptive Media Trailer is capable of piloting four adsorptive media filters in a side-by-side comparison using identical raw water and pretreatment conditions. The trailer has individual control of flow rates, as well as continuous monitoring of pressure loss and turbidity of each filter. The trailer measures 14’L x 8’W x 7’H and uses a single 20Amp 120V electrical supply. The pilot system is equipped with a pressure reducing valve (PRV) on the raw water supply line and requires 10 gpm at 45 psi.
The raw water is chemically pretreated, and then distributed to four filters by a common manifold. Four filters may be operated simultaneously during the pilot. Each filter is equipped with a system of four motorized ball valves that allow for automated control of filter service and backwash cycles. Two programmable timers control the motorized valves. The timers operate in lead/lag mode, with one timer dedicated to the filtration cycle, and the other timer dedicated to the backwash cycle. The system can also be operated in manual mode.
Each filter has a dedicated rotameter and globe valve to control flow rates, with a pressure reducing valve installed upstream of the flow control valve in order to maintain a constant discharge pressure, and prevent declining flow operation. Excess filtered and backwash water is discharged to a sample sink, and drained to waste on site by gravity.
Finished water from each filter is sampled at the point of discharge to the sample sink. Source water is sampled from a port at the inlet to the pilot system. Chemically pretreated water could be sampled from a port on the inlet to any of the four filters. Raw water and pretreated water samples discharged continuously to the sample sink, at flow rates of about 200 mL/minute.
The pilot trailer includes a PC based data acquisition system for monitoring turbidity and pressure of the raw water and the filter effluent flows. Turbidimeter flows are monitored and discharged continuously to the sample sink, at flow rates of about 200-500 mL/minute.
Adsorptive Drawing
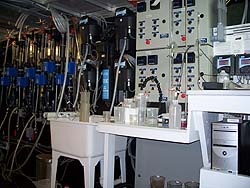
2. Bench-Scale / Jar Testing Trailer
This portable Bench-Scale / Jar Testing Trailer is for the evaluation of chemical pretreatment, and coagulation and sedimentation needs. The trailer is equipped with a four-position Phipps Bird Jar tester, streaming current monitor, and all necessary field equipment to monitor and control the water or wastewater chemical treatment and coagulation system. Stock chemicals are provided by several chemical suppliers, so the evaluation of potential treatment alternatives will remain competitive. The trailer is 16’L x 8’W x 11’H and uses a single 20Amp 120V electrical supply. Continuous pilot water supply is not required.
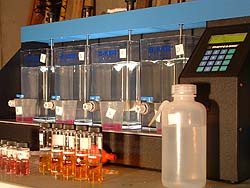
3. IDI Ferazur / Mangazur Trailer
This portable Ferazur / Mangazur Trailer is capable of piloting an Infilco Degremont Technologies process that uses an inert media for the organic removal of iron and manganese. The trailer has individual control of flow rates, as well as monitoring of pH, temperature, flowrate, pressure loss and turbidity of each filter. The trailer measures 16’L x 8’W x 11’H and uses a single 20Amp 120V electrical supply. The pilot system is equipped with a PRV on the raw water supply line and requires 10 gpm at 45 psi.
The pH and dissolved oxygen of raw water are balanced prior to distribution to the first filter for biological iron removal. The filter effluent is then re-balanced for pH and DO prior to being fed to the second filter for biological manganese removal. Each filter is equipped with a system of four manual ball valves that allow for automated control of filter service and backwash cycles.
Each filter has a dedicated rotameter and globe valve to control flow rates, with a pressure reducing valve installed upstream of the flow control valve in order to maintain a constant discharge pressure, and prevent declining flow operation. Excess filtered and backwash water is discharged to a sample sink, and drained to waste on site by gravity.
Finished water from each filter is sampled at the point of discharge to the sample sink. Source water is sampled from a port at the inlet to the pilot system. Chemically pretreated water could be sampled from a port on the inlet to any of the filters. Raw water and pretreated water samples discharged continuously to the sample sink, at flow rates of about 200 mL/minute.
The pilot trailer includes a PC based data acquisition system for monitoring pH, temperature, flowrate, turbidity and pressure of the raw water and the filter effluent flows. pH monitoring is used to control the pace the chemical metering pumps. Turbidimeter flows are monitored and discharged continuously to the sample sink, at flow rates of about 200-500 mL/minute.
IDI Drawing
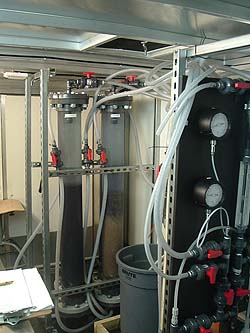
4. Ozone Testing Trailer
The Ozone Testing Trailer is equipped with a Pacific Ozone generator; recycle pump; injection nozzles; ozone contact tanks; ozone quench system and quenching tank, and two pilot filters. Trailer is 16’L x 8’W x 11’H and uses a single 20Amp 120V electrical supply. Pilot water supply requires 10 gpm at 45 psi.
The ozone generator and injector assembly are capable of providing 14 grams O3/hr, and contain a 5-gallon ozone contact tank. The ozone is injected into the flow stream using a Mazzie injector. The water then flows into the contact tank that provides up to 30 minutes of contact time. Sodium Bisulfite may be added to the water to quench any ozone remaining in the water, and the water passed through an ozone quench tank with 7.5 minutes of detention time. The pilot water is then fed into the pilot filters.
Two Biologically Activated Carbon pilot columns are installed with sufficient pipe, valves, meters and miscellaneous parts as required to operate in filtration mode for a preset run time. The backwash then occurs automatically. Both filtration and backwash flow rate are set using globe valves and rotameters set during the optimization period.
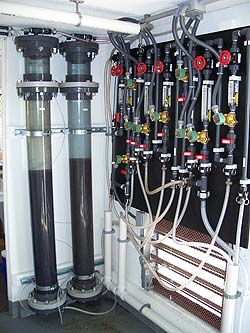
5. Conventional Treatment Trailer
The Conventional Treatment Trailer is equipped with mixers, chambers and a settling basin. The trailer is 16’L x 8’W x 11’H and uses a single 20Amp 120V electrical supply. Pilot water supply requires 10 gpm at 45 psi.
A chemical pretreatment system allows for injection of various chemicals using either peristaltic or diaphragm metering pumps with a static mixer located downstream of the chemical injection ports. The chemically pretreated water first enters the rapid mix chamber, and then flows through as many as three successive mix chambers before entering the settling basin. Perforated lexan plates separated the individual mix chambers and settling basin.
Each mix chamber holds a volume of 50 gallons, and is equipped with an adjustable rate mixer with two 1” x 10” vertical paddles. From the rapid mix chamber, the water flows into a subsequent slow mix chamber, and then into the settling basin, which holds a volume of 200 gallons, and has a surface area of 10 square feet. The settling basin is equipped with seven parallel settling plates with 2 inch spacing between adjacent plates, set at an angle of 60 degrees with the horizontal. The plates force the flow upward through a cross sectional area of 1 square foot for a distance of about 20 inches, such that no particle will have to settle further than 4 inches before encountering one of the plates. Settled flocculants collect in the lower portion of the settling basin, from which the settled sludge can be periodically drained.
The settling basin effluent overflows into a horizontal discharge pipe that spans the tank above the settling plates. The discharge pipe has a series of openings along the top surface, and acts as a weir to maintain a constant water level through the settling basin and mixing chambers. The discharge pipe drops to the settling basin sump, from which a portion of the settled effluent is re pumped to the sand filters, and the balance overflows by gravity to a waste sump.
Two filters are arranged in parallel, and are supplied with pressurized water pumped from the settling basin sump. Filter inlet pressures are monitored by a common gauge on the line that supplies settling basin effluent to both filters. The filter columns are constructed of 6 inch diameter clear PVC, flanged at top and bottom, with bulkhead fittings through the flanges for the inlet (top) and outlet (bottom) piping.
Conventional Drawing
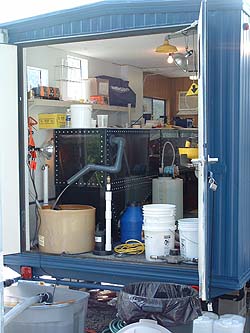
6. Emergency Chemical Feed Trailer
This Emergency Chemical Feed Trailer is capable of providing long term non-permanent chemical feed for water and wastewater treatment facilities. Although easily adapted, the trailer is traditionally used for disinfection purposes. The trailer measures 16’L x 8’W x 11’H and uses a single 50Amp 120/240V electrical supply.
The treatment facility’s motive water is connected to the trailer where chemical (typically sodium hypochlorite) is injected via chemical metering pumps. The chemically treated water is returned to the facility.
The motive water has a dedicated rotameter and globe valve for flow control, with a pressure reducing valve installed upstream of the flow control valve in order to maintain a constant discharge pressure. The pumps are equipped with manual speed and stroke adjustment and are calibrated over the full range of operation on site prior to commissioning. The trailer includes climate control.
Items often required, but typically provided by the Owner or Contractor:
- Chemical storage
- Eye wash station
- Containment facility
- Site security
- External piping and wiring
Emergency Drawing
 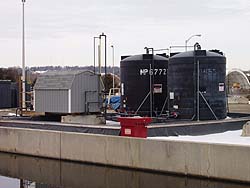
7. Mobile Pilot Kits
A Mobile Pilot Kit (MPK) is a self contained portable pilot testing facility enclosed in a shipping case measuring about 2’ x 2’ x 6’, which includes a pilot test filter and all the equipment required to perform chemical pretreatment of the source water, and to monitor and control flow rates during both filtration and backwash cycles.
Each MPK contains: a vertical 5 foot tall pilot filter column constructed of 6 inch diameter clear PVC, equipped with an inlet structure at the top and an underdrain system at the bottom; a chemical feed system including three diaphragm metering pumps, each with a 2.5 gallon chemical reservoir; an in line static mixer to ensure proper mixing of the injected chemicals; a 0.5-5.0 gpm rotameter and globe valve installed on the effluent side of the pilot column to control flow rates during filter service. A PRV is on the effluent side of the filter to maintain constant pressure and steady flow rates during filter service. There is a 0.5-5.0 gpm rotameter and a globe valve to control flow rates during backwash; two pressure gauges (0 to 100psi), one each on the filter inlet and outlet, to monitor pressure losses across the filter; a control system for automated operation on a timed cycle of filtration and backwash.
The MPK control system consists of two programmable timers operating in lead/lag mode, each timer controlling 2 motorized ball valves. One timer is dedicated to the filtration cycle, while the other timer is dedicated to the backwash cycle. The filter and backwash flow rates are presets both using the rotameter globe valves. Each motorized valve has hand/auto/off settings for manual or automatic control.
MPK Drawing
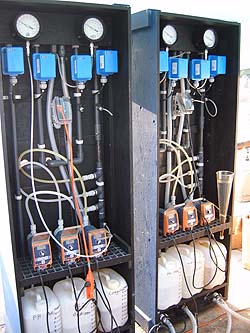
8. Vendor-Supplied, Rental, and Generic Pilot Equipment
Blueleaf often operates pilot equipment rented from equipment suppliers. Blueleaf can also provide process equipment that is required by the pilot, but may not be included in the Vendor’s scope of work. Coordination with the equipment vendor for delivery, unloading and set up of electrical and process piping can be included.
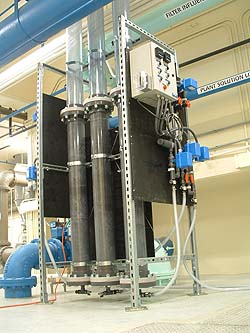
|
|